BAYDUR: Industrial Design discovers new forms
- Av Consulting SNC
- 5 ott 2016
- Tempo di lettura: 2 min
The material used in the moulding process is called Baydur®, a thermosetting polymer produced and distributed by the company Bayer Material Science.

Baydur® 60
Baydur® 60 is a medium-density structural polyurethane, which by virtue of its sandwich structure – a compact external skin with a foam core – opens a wide range of design possibilities. This polyurethane system is particularly well suited to the production of large size mouldings. The moulded elements can sustain thicknesses of 4 - 20 mm at densities between 500 and 700 kg/m3.
Baydur® 110
Baydur® 110 is a compact microcellular engineered polymer for reaction-injection moulding (RIM), with a density of 1050 - 1150 kg/m3, notable primarily for being highly economical to work with. Its short ejection cycles make it possible to produce articles at competitive costs which are mainly between 4 and 6 mm thick and have high stiffness and mechanical strength. The use of aluminium equipment offers high competitiveness in equipment costs; finally, the production process conforms to environmental standards.
Features of Polyurethane:
✔Excellent resistance to mechanical stress
✔Good surface hardness
✔Highly flame-resistant, if treated with halogen-free fireproofing products.
✔Outstanding weather resistance
✔It is always free of sink marks and deformations, even when used with ribbing and reinforcers, thus offering an excellent aesthetic finish
✔Guaranteed chemical inertness on contact with many organic and inorganic substances (include the most common acids)
✔Offers excellent electrical and thermal insulation properties
✔Presents a surface which is ideal for painting with any kind of coating, including conductive finishes
✔It can be moulded in colour
✔It allows metal and non-metal inserts to be embedded inside the manufactured article during the process of moulding, to support fixings and reinforcers
✔It can be disposed of as an inert, non-hazardous waste
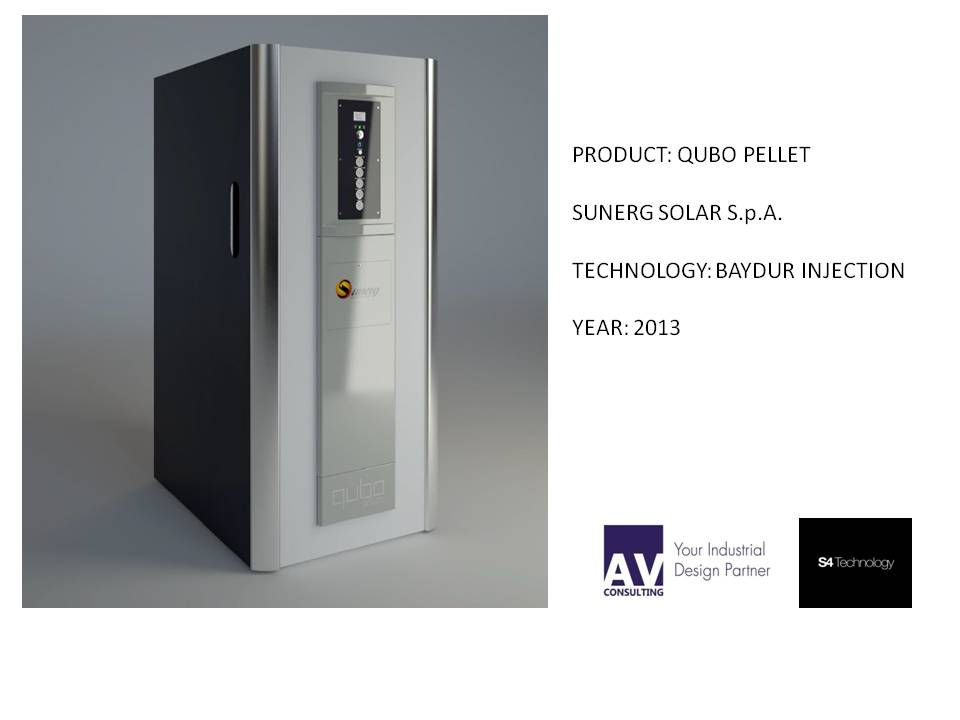
Advantages of Polyurethane
✔The ability to achieve variable wall thicknesses
✔Support for highly complex geometries, adding value to the design of the moulded product
✔Exceptional accuracy in the reproduction of series of parts of large, medium and small sizes
✔Highly durable and lightweight product
✔High surface quality, allowing a superb paint finish
✔The option of embedding inserts inside the product during moulding
✔The use of aluminium moulds, which are cheaper than the steel ones used in other injection moulding processes
✔Short forming time
✔Flame-retardant to V-0 standard, UL certified: www.ul.com
Market areas of application include but not limited to medical, automotive, heavy equipment, sports, liesure and agriculture.
At AV Consulting, we specialize in large format complex molding of device covers, enclosures and housings. Our RIM with polyurethane (PUR) process allows the designer to design for both sides of the part enabling them to incorporate cost saving ideas for part count reduction, DFA concepts and post mold operations.
Our pur material selections allow for large format parts to be molded in a single shot (up to 85 lbs. or 6' x 6' x 2'). Multiple wall thickness in a single part can be realized without sink or distortion so you can have a quarter inch wall section next to a 2" wall without issue. We also offer flexible and impact materials as well for harsh environmental conditions.
Comments